1.What’s a ring main unit gas tank?
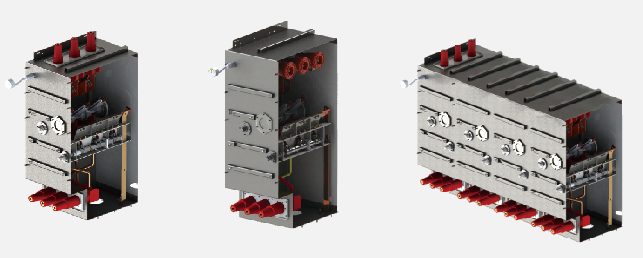
2.Materials of the Ring Main Unit Gas Tank
3.Processing of the Gas Tank
4.Placement of Electrical Components in the Gas Tank
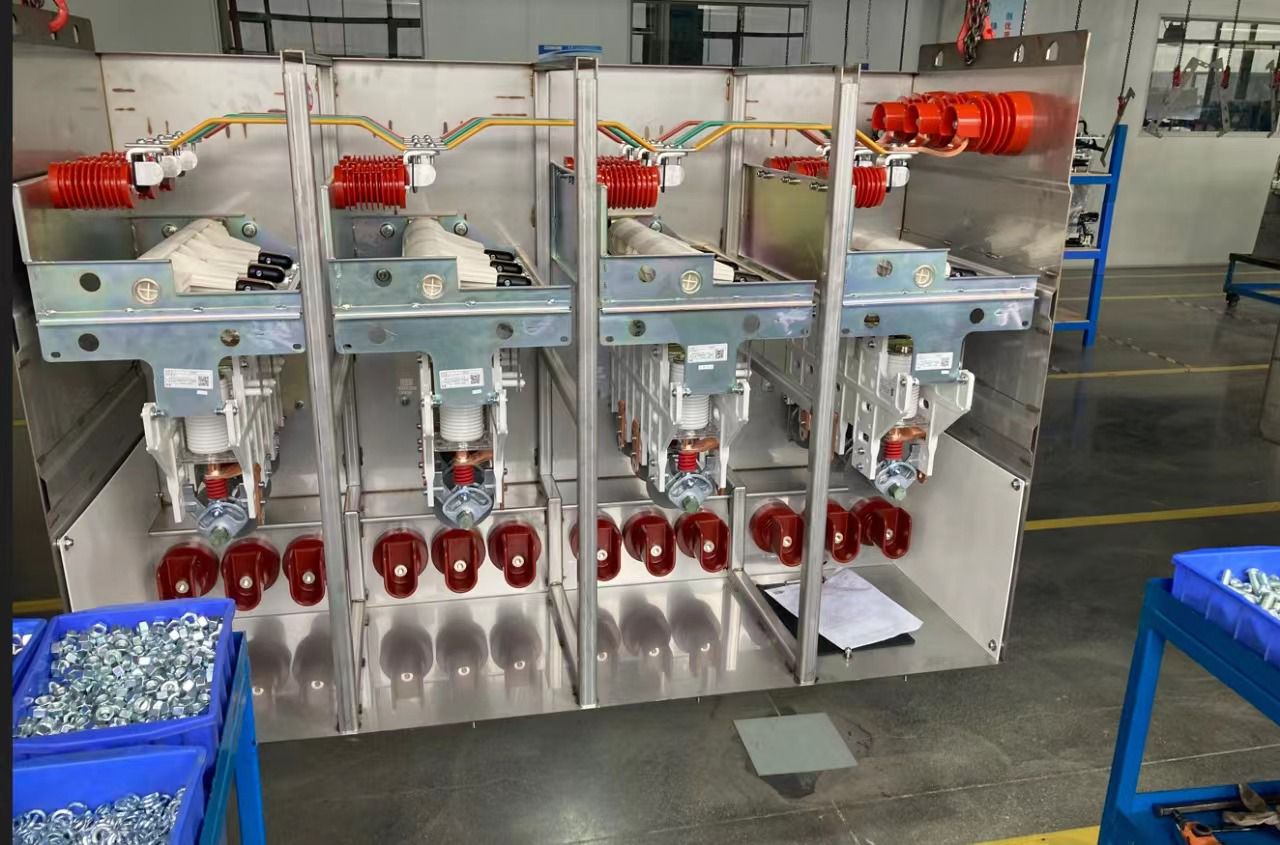
5.Types and Characteristics of Gases in the Gas Tank
Gas Types:
The insulating gases in the ring main unit gas tank mainly include sulfur hexafluoride (SF6), dry air, nitrogen, and their mixtures. SF6 gas has excellent insulation and arc – extinguishing properties. Its insulation performance is 2 – 3 times that of air. Under the same electrical clearance, using SF6 gas can make the equipment smaller. However, SF6 gas is a greenhouse gas and has a certain impact on the environment. Therefore, the application of environmentally friendly gases has been gradually promoted. Dry air is easy to obtain, and nitrogen has stable chemical properties. Under certain pressure and electrical clearance conditions, they can also provide good insulation performance and have become viable alternatives to SF6.
Working Pressure Range:
The working pressure ranges of different insulating gases are different. The design pressure of SF6 gas in the ring main unit gas tank is generally between 0.02 – 0.05 MPa (gauge pressure). Within this pressure range, SF6 gas can maintain good insulation and arc – extinguishing performance and also helps to evenly distribute the electric field inside the gas tank, reducing the risk of partial discharge. For dry air and nitrogen, due to their relatively weaker insulation performance, the design pressure is relatively lower, generally around 0.01 – 0.03 MPa (gauge pressure). The lower pressure design takes into account both cost factors and the ability to meet basic insulation requirements, ensuring the safe and economical operation of the gas tank.
6.Connections and Interfaces with the Outside
Cable Interface:
The gas tank is equipped with a dedicated cable interface for connecting incoming and outgoing cables. These interfaces are exquisitely designed and adopt effective sealing measures, such as rubber sealing sleeves, which can effectively prevent external moisture, dust, and other impurities from entering the gas tank, ensuring the cleanliness and safe operation of the internal electrical components. At the same time, the design of the cable interface fully considers the adaptability of different cable specifications. By installing suitable sealing rubber rings and adapting to different sizes of cable terminals, it can be conveniently connected to various cable models, ensuring good electrical connection between the cable and the electrical components in the gas tank. In addition, the aperture and shape of the interface are optimized to ensure that the electric field distribution at the interface is uniform when inserting and fixing the cable, effectively avoiding the occurrence of partial discharge.
Operating Mechanism Interface:
The operating handle and other operating mechanisms outside the gas tank need to be accurately connected to the internal switch and other electrical components. Corresponding interfaces are set on the gas tank wall, and the external operating force is smoothly transmitted to the internal electrical components through mechanical components such as transmission shafts and connecting rods. When designing these interfaces, it is necessary to ensure the effective transmission of the operating force so that the operator can accurately control the operation of the internal switch and also ensure the sealing of the gas tank to prevent gas leakage. For example, when operating the load switch, the operator rotates the external operating handle, and the operating force is accurately transmitted through the sealed interface on the gas tank wall and the internal transmission shaft, driving the contact of the load switch to complete the opening and closing actions. The whole process is efficient, safe, and reliable.
7.Protection Level of the Stainless Steel Gas Tank
8.Advantages and Disadvantages of the Stainless Steel Gas Tank
Advantages
Strong Corrosion Resistance:
The chromium, nickel, and other alloy elements contained in the stainless steel material endow it with excellent corrosion resistance, which can effectively resist the erosion of various media such as the atmosphere, water, acids, and alkalis, is not easy to rust, and significantly extends the service life of the gas tank. It is especially suitable for harsh environments with corrosive gases or liquids, such as the application of power equipment in the chemical and marine fields.
High Strength:
It can be used in occasions with high requirements for structural strength, such as the storage or transportation of high – pressure gases. It has relatively high strength and hardness and can withstand a certain amount of pressure and impact force. It is not easy to deform or damage under various complex working conditions, effectively ensuring the safety and stability of the gas tank during use, providing a solid guarantee for the reliable operation of the power system.
Good Sealing:
The stainless steel material is convenient for achieving excellent sealing effects through welding, sealant, and other methods, effectively preventing gas leakage and ensuring the stability of the gas pressure in the gas tank. This is crucial for applications with extremely high sealing requirements, such as gas storage tanks and high – voltage switchgear, ensuring the normal operation of the equipment and the safety of operators.
Good High – Temperature Resistance:
Some stainless steel materials have good high – temperature resistance and can maintain stable performance within a certain temperature range, meeting the usage requirements in some high – temperature environments, such as the application in industrial heating furnaces, boilers, and other equipment, providing reliable protection and support for power equipment in high – temperature environments.
Long Service Life:
Considering its advantages such as strong corrosion resistance, high strength, and good stability, the stainless steel gas tank has a long service life, reducing the cost and inconvenience caused by frequent equipment replacement. In the long term, it reduces the overall operating cost of the equipment and improves the cost – performance ratio of the equipment.
Disadvantages
High Price:
Compared with some ordinary material gas tanks, the manufacturing cost of stainless steel is relatively high, resulting in a relatively expensive price of the stainless steel gas tank. To a certain extent, this increases the initial investment cost of the project and may affect its selection and application in some cost – sensitive projects.
Heavy Weight:
The density of stainless steel is relatively large, making the stainless steel gas tank relatively heavy. During the installation, handling, and transportation of the equipment, more manpower, material resources, and time are required, bringing certain inconveniences to the construction and maintenance and having a certain impact on the efficiency and convenience of installation and maintenance.
Difficult Welding:
The welding performance of stainless steel is relatively poor, and relatively high requirements are placed on the welding process and technology. Professional welding equipment and experienced and skilled operators are required for operation. Otherwise, welding defects such as pores, cracks, and slag inclusions are prone to occur, which will seriously affect the quality and sealing of the gas tank and then endanger the safe operation of the equipment.